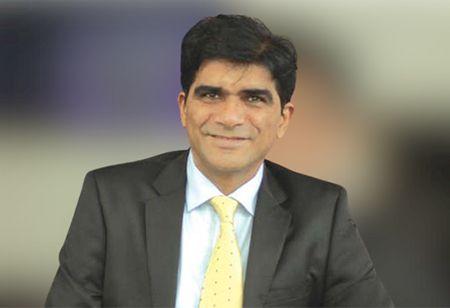
Simulation: The Shortest Route Between Design & Reality
In the present-day scenario where the race for innovation is constantly on and competition is like never before, the traditional ways of product development is no longer sufficient. Simulation that used to be an occasional resource applied in the design of only the most complex engineering products is today becoming pervasive i.e. it’s a continuous simulation with all physics across the entire lifecycle, for all kind of products. Simulation has become a standard component in product development today that is bridging the gap between design and reality.
The Design Journey
Engineers are under pressure to design innovative products that work perfectly the very first time itself in order to be able to get them out into the market before the competition does so. Additionally, they need to be sure that the product will endure and be reliable once it enters the market. Simulation solutions involving any area of physics, be it structures, fluids, electronics or combinations of these, will provide engineers with the speed that is needed to stick to these goals that seem to be almost impossible to reach. The toughest design challenges can be overturned and made into a success story with engineering simulation software. Simulation of the design helps in the validation and the verification of the function of the product and engineers can check product feasibility too.
Faster, Simpler & Cost Effective
Simulation accelerates design to an extend that is almost unbelievable. Engineers are now even able to see the real-time results of simulation throughout the modeling process and this enables them to understand all the design changes in their prototypes. Simulation is providing engineers with unparalleled understanding into their design implementations. Engineering simulation is becoming more pervasive in its ability to positively impact product innovation and performance, time to market, drive top-line growth, reduce cost and deliver end-user benefits. The integrated Multiphysics platform of simulation provides customers the capability to innovate and analyze designs across all the different physics and this goes for all products, not only complex ones. Using simulation more ubiquitously and pervasively will simplify tasks and allow engineers to take decisions earlier on thereby reducing the cost of production.
We have been helping drive this innovation with engineering simulation, while also reducing costs and product development time. Simulation-driven design solutions like Discovery Live offer a unified modeling and simulation environment and remove the limitations between CAD and simulation Instantaneous simulation is tightly coupled with direct geometry modeling, to enable interactive design exploration that permits design engineers to better understand each of the many design decisions they make during product development course. Supporting common fluids, structural, and thermal simulation applications, it allows engineers to experiment with design ideas and see instant feedback from their changes. It therefore radically lessens the need for persistent, laborious testing on expensive physical prototypes and consequently cuts the total development time and cost.
Additive Manufacturing
The design engineer today needs to build optimized, lighter and smarter products to stay relevant. With additive manufacturing, the process of manufacturing itself can introduce changes in the final shape, and simulation can help to factor in those changes. Therefore, there is a need to use appropriate tools like 3D Design products that enable CAD modeling and simulation for all design engineers. Simulation tools are today built on direct modeling technology that makes creating, repairing or editing geometry easy, whether you are involved in concept modeling, reverse engineering scanned data or preparing a model for manufacturing or simulation.
Digital Twin and Simulation
During operation, to fully comprehend a machine, the comprehensive virtual model must be connected to actual operational data from the machine. The virtual model is the digital twin. Digital twins eliminate the silos, errors inadequacies, doubts and enormous resources while working with models. Engineering simulation forms a key component of the digital twin. When simulation is added to the digital twin system, environments that are otherwise difficult to view and evaluate becomes evident. The product performance can be maximized by scheduling predictive maintenance, determining root of performance is sues, and evaluating various other aspects. Simulation allows accurate prediction of how the changes in machines will affect it during its life cycle. Simulation is thus the lone method to completely appreciate the digital twin technology.
On-Product Simulation
From cars, airplanes and trains to consumer electronics, machinery and healthcare solutions, products have been transformed through simulation. Product simulation observed single characteristics: one physics, one component, one design. Now we explore multiple designs at the system level with interactions across several physical and digital realms. Simulation is being utilized not only for design validation, but also from early ideation through manufacturing, operations and maintenance. We are thus viewing an ultimate revolution in engineering and product development. The advantages of simulation when in vehicles are well-known. As on-track testing is expensive and not always feasible, simulation is what makes design changes easier and makes it a reality.
Autonomous cars, for example, have to be out on the open road and be able to adapt to all the uncertainties that come along with it. It has to have the ability to do this on par with or even better than humans in order to be considered safe. What is required is over eight billion miles of test driving. How does a company do so much testing? The only solution is simulation if one is hopeful of releasing them anytime soon. The validation of the software that is needed by the manufacturers can be done only in this manner. If one depends exclusively on AI for autonomous cars then one won’t be able to assign or trace the neural networks of AI to safety requirements.
Simulation actually trains and tests artificial intelligence. The safety gates of autonomous car developers are what decide if the outputs of the AI system disrupt any safety standards. If positive, then it initiates a course of action based on a safety plan. This system needs to be validated and the only way to do that in less time is through simulation. There is a seamless integration of design and simulation for all engineers now that help them to explore ideas and concepts in greater depth. It provides a single platform for simulation-driven product development. The technology is easy to learn and use and offers unparalleled adaptability, speed and accuracy to enhance the final design. Simulation is thus the shortest route between design and reality and it helps companies in bringing innovative and safer products into the market faster.