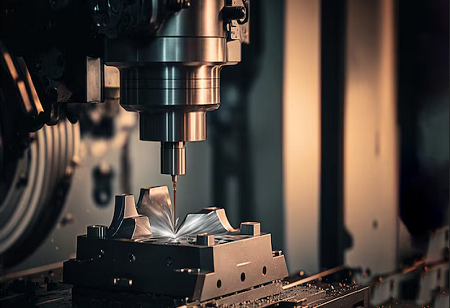
From Prototype to Production: Optimizing CNC Machining Workflows
A renowned leader in the manufacturing solutions landscape - Mitsubishi Electric India has recently unveiled its latest innovation, the M80LA model of Computerized Numerical Controllers (CNCs), which was designed specifically for the turning segment. With an aim to improve manufacturing efficiency & productivity, cutting-edge technology has been integrated into the M80LA model.
Kazuhiko Tamura, Managing Director, Mitsubishi Electric India shared the organization’s commitment to advancing manufacturing excellence in India via the M80LA CNC model launch. S. Sriram, Director of FAID Division highlighted the transformative capabilities of the model and emphasized the dedication of Mitsubishi Electric India’s dedication for driving technological innovations in manufacturing. Masaya Takeda, General Manager of CNC Systems underscored the importance of the new CNC system in revolutionizing the Indian manufacturing sector, buttressing automation, digitization & the country’s journey towards self-reliance.
Optimizing Computer Numerical Control machining workflows is crucial to improve efficiency, ensure high-quality output, & decrease costs right from prototyping to full-scale manufacturing. This comprehensive approach comprises best practices as well as strategies across numerous phases of the CNC machining process. This includes design optimization, tool path generation, machinery set up, process monitoring, quality control as well as workforce development. Every step should be planned meticulously as well as executed for achieving the best results.
Design optimization
The base of any efficient CNC machining workflow is Design optimization. This is because a well-optimized design can help in decreasing the machining time, enhancing quality as well as lower costs. What is crucial here is the concept of Design for Manufacturability (DFM). Simplifying part geometries facilitate in minimizing the various machining operations that is needed. Eliminating intricate features which necessitate specialized tools or even complex setups can streamline the processes.
Moreover, making sure that all features are accessible by some of the standard cutting tools removes the requirement for custom tooling, thereby, reducing production times & costs. Another critical factor is material selection and materials should balance machinability as well as the needed mechanical properties with common choices such as aluminum rendering ease of machining when compared to more challenging materials like titanium or stainless steel.
Specifying realistic tolerances which are achievable with standard CNC machining processes is equally crucial. While surface finish requirements have to meet certain functional requirements without adding unwanted complexities, overly tight tolerances can increase the machining time as well as costs unnecessarily.
Prototyping
Testing & refining designs is highly crucial for ensuring they meet all the necessary specifications as well as performance criteria prior to moving to complete-scale manufacturing in the prototyping phase. Additive manufacturing or 3D printing is one of the prototyping techniques which can quickly elevate form & fit, letting for faster iterations. CNC machining is the preferred methods for prototypes that need precise dimensions as well as material properties.
An iterative design process and the feedback from prototype is used for refining and enhancing the design which can save enormous amount of time as well as resources. This particular process most often comprises several iterations with functional tests that are performed on every prototype for ensuring they meet performance requirements. Adjustments which are based on these test results not only facilitate in perfecting the design but they also ensure it is robust & ready for manufacturing.
Toolpath Generation
One of the critical aspect of CNC machining which can influence the efficiency as well as quality of manufacturing processes. Advanced CAM software like SolidCAM, Mastercam & Fusion 360 can create optimized toolpaths and for cutting tools this ensures the most efficient routes.
Machine setup & Calibration
Proper machine setup & calibration are highly essential for achieving precise & consistent machining results. Robust fixturing solutions are needed for securely holding the workpiece, ensuring repeatability & reducing vibrations. Modular fixturing systems can also be implemented for reducing setup times when switching between different components.
Some of the top CNC manufacturers in India include Aaradhana Technology Systems, Trilok Lasers, Jai Industries, Mehta India, Jyoti CNC, Om CNC Automation, Tirupati CNC Machine, Mohan Industries and others.
Process Monitoring & Control
This process plays a huge role in maintaining high productivity as well as part quality. Immediate feedback is provided by real-time monitoring systems that are used for tracking machine performance, part quality utilizing sensors, tool wear, as well as IoT devices which allow for quick adjustments.
Ensuring the quality of machined parts is crucial at every phase of the CNC machining processes, which makes Quality Control & Inspection highly essential. Probing – the In-process inspection techniques can help in checking critical dimensions during the machining process allowing for immediate adjustments. Comprehensive post-process inspections using CMMs & various other metrology equipment to verify that parts can meet specifications before the products being shipped to the customers.
Optimizing CNC machining workflows right from prototyping to manufacturing comprises a comprehensive approach which addresses a set of processes which include phases from design optimization to process monitoring to supplier management. Through the implementation of best practices in every segment, manufacturers can achieve remarkable enhancements in efficiency, cost-effectiveness as well as product quality. Continuous evaluation as well as adaptation of these practices is important for keeping pace with advancements in CNC technology as well as evolving market demands. This holistic approach makes sure that CNC machining operations stay competitive as well as capable to meet the highest precision & productivity standards.